BISO 3D - CHASIS HÍBRIDO
EL CABEZAL 3D VARIOFLEX AIR i UTILIZA LA 3ª GENERACIÓN DE CHASIS HÍBRIDO
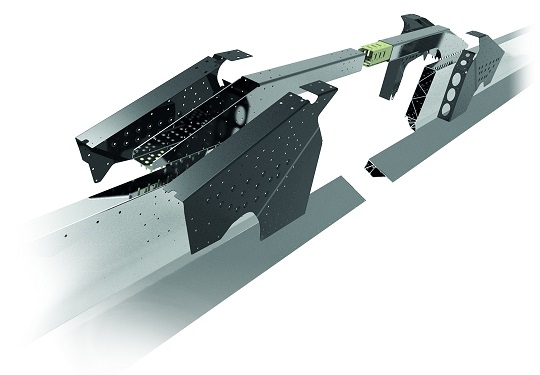
La cuestión clave para una larga vida útil de un cabezal es un chassi fuerte y un buen carro para el transporte. El cabezal de alta calidad no será reconocido después solo de un año en servicio, pero después de 10.000 ha cosechadas y miles de kilómetros en el carro de transporte. El cabezal de acero funciona bien hasta un máximo de 9 m de anchuras. Y nuestros chasis de acero aparentemente sobreviven más que los otros. La única solución para tener un chasis sólido para cabezales anchos es algo que nosotros en BISO, después de años de investigación y desarrollo, llamamos CHASIS HÍBRIDO.
BISO ULTRALIGHT UL1230 y nuestra cosechadora CR9090 SmartTrax. La larga vida útil está relacionada con un chasis fuerte ... chasis híbrido (foto de la sucursal BISO HURBANOVO, Eslovaquia).
Ya con un ancho de 8.5-9.0m, el chasis de acero se resbala tanto que la durabilidad de los rodamientos del sinfin y todos los componentes de la transmisión sufren. Para los chasis híbridos que combinan aluminio y acero, la compresión es mínima y el cliente evaluará sus ventajas después de algunos años de trabajo. Las ventajas de esta tecnología se pueden ver en los cabezales con una anchura de aproximadamente 12 m. Utilizamos esta tecnología por la primera vez en los cabezales Ultralight de tercera generación y los clientes apreciaron el beneficio real de esta tecnología después de algunos años de trabajo. El chasis HÍBRIDO extremadamente fuerte es también el requisito básico para un sistema VARIO que funcione bien con una extensión de 800 mm y la posibilidad de colocar las cuchillas de corte justo debajo del sinfín de alimentación. La distancia mínima entre las espirales del sinfín de alimentación y las cuchillas de corte es de solo 170 mm.. Y este es una caracteristica que le interesa durante la cosecha de cebada extremadamente corta.
El diseño de la sección central de un chasis híbrido que ya se encuentra en el cabezal 3D VarioFlex AIR i (foto realizada durante las pruebas en 2018).
El camino hacia el chasis híbrido fue significativamente largo y comenzó ya en 2007
En la Feria Agritechnica 2007 en Hannover, presentamos el cabezal BISO VX1200 CropRanger PremiumPlus con un anchura de 12 m. Este era el cabezal con un chasis de acero y con el módulo FLEX. Por razones de peso, el cabezal estaba equipado con ruedas de soporte suspendidas por aire. Esto significa que la cosechadora debia empujar el cabezal en lugar de sostenerlo. Llamamos a esta solución como la Ultralight de primera generación y la primera experiencia con ella nos mostró que este no es el camino a seguir. Ya en 2009, BISO recibió una medalla de plata por el primer cabezal de aluminio, con la UltraLight 800 en la feria Agritechnica. Este cabezal tenía un chasis completamente de aluminio que incluía también las paredes laterales. Una característica interesante de este cabezal fue el chasis seccional hecho de módulos, que fueron pegados y atornillados. Se suponía que la principal ventaja del diseño en sección eran las reparaciones fáciles en caso de daños en alguna parte del cabezal. Las anchuras oferta (770, 870, 990, 1050, 1200, 1290, 1420) también se basan en la combinación de los módulos. En 2011, la estructura de los modelos más grandes 1070, 1200, 1290, 1410 fue actualizada con un nuevo diseño.
Agritechnica 2007: ruedas de soporte con suspensión neumática y totalmente integradas en el cabezal de 12 metros con un chasis de acero. Presentamos el mismo cabezal a nuestros clientes en la feria Techagro 2008 en Brno.
Agritechnica 2007: el primer intento con un cabezal de 12 m de ancho, el CropRanger VX1200 Premium Plus qué ya estaba equipado con el módulo FLEX.
Estamos viendo el mismo cabezal con cuchillas integradas en el chasis. De interés el accionamiento central del sinfín y del molinete divididos de forma no simétrica. El chasis de acero era el límite principal de este diseño y abandonamos esta solución por varias razones.
A finales de 2012, comenzó la producción del Ultralight de tercera generación con un chassis completamente nuevo a partir de perfiles de aluminio llamados "sandwiches" en combinación con piezas de acero (por ejemplo, la sección central del corte en conexión con la garganta de la cosechadora). Y este nuevo chasis fue llamado CHASIS HÍBRIDO gracias a la combinación de aluminio y acero. En la lista de precios de 2013, aparecieron tres modelos: 1070, 1220 y 1410. En 2013, este nuevo modelo Ultralight de tercera generación fue exhibido en la feria Angritechnica en Hannover con el apelido de NUEVO ULTRALIGHT. Los cabezales producidos tienen paredes laterales de aluminio (la transmisión suele ser de ambos lados) para ahorrar cada kilogramo de peso. El principal mercado para esta categoría de cabezales siempre ha sido Alemania, donde la mayoría de ellos ha sido vendido. Los modelos Ultralight de segunda y tercera generación trabajan en el Reino Unido, Australia y Canadá. Otros mercados importantes son la República Checa y Eslovaquia. Los clientes que han estado trabajando con estos productos durante 5 años y más aprecian el chasis robusto y la larga vida útil de todos los componentes. Los modelos Ultralight de segunda generación ya tenían un chasis extremadamente fuerte, pero gracias al chasis híbrido, la tercera generación ganó una resistencia extrema comparada contra la competencia y, por consecuencia, todos los componentes obtuvieron una vida útil significativamente más larga como los rodamientos y el sinfín.
Un diseño interesante del chasis híbrido en el cabezal ULTRALIGHT UL1070 equipado con el módulo FLEX de primera generación ya en 2014 (foto de las pruebas de fábrica en Eslovaquia).
La imagen del chasis durante la prueba de las primeras versiones de 3D VarioFlex. El sistema del rodamiento central del sinfín y la disposición de los accionamientos ya no cambian fundamentalmente. (BISO Hurbanovo, Eslovaquia 2017).
Para la temporada 2014, dos modelos de Ultralight 1070 y 1230 ya estaban listos para la producción en combinación con el carro ProfiSteer con un eje trasero orientable (para cabezales con un anchura superior a 12 m es imprescindible). Para la temporada 2015, ampliamos nuestra oferta gracias a los modelos 770 y 920 con transmisión de un lado, mientras los modelos 1070 y 1230 se mantuvieron sin ningún cambio. La Ultralight 920 generalmente se produjo con transmisión doble por razones de unificación de producción. Esta solución se hizo muy popular entre los clientes que cosechan con un ancho de 9.2 (cada caja de engranajes maneja chuchillas de solo 4.6m de largo). Los conductores elogian esto a pesar del control de mantenimiento matutino que debe hacerse con las unidades en ambos lados.
Esquema del chasis híbrido: el resultado de más de 10 años de pruebas intensivas. Estamos trabajando en la tercera generación ahora. Los chasis se calculan para anchuras de 18 m.
Al final, el diseño del chasis seccional no aportó la ventaja de servicio
Al comienzo se tuvo la decisión de que, al igual que en la industria automotriz, la solución correcta sería el uso de aleaciones de aluminio y inmediatamente surgió una discusión: ¿Qué pasa con el servicio en el campo? ¿Cómo repararemos el daño del chasis? Por esta razón, utilizamos una solución seccional con la idea de cambiar solo el módulo roto en caso de un accidente con algún obstáculo. Nuestra experiencia y práctica es tal que si golpea un obstáculo con el cabezal de acero, podemos repararlo. Sin embargo, si el cliente tranfiere el cabezal a la fábrica BISO, nosotros podemos desmontar todas las piezas mucho más rápido y de una manera mucho más efectiva y reparar el chasis a nivel profesional. Todavía muchas veces la reparación no es rentables y producir un nuevo chasis suele ser más barato que reparar el antiguo. Entonces, con la introducción del chasis híbrido, basado en la experiencia adquirida, ya no nos enfrentamos al problema de la reparación.
Las pruebas de la sección central (el lugar, donde las secciones izquierda y derecha se superponen) son generalmente muy importantes si el módulo FLEX está activado. En la imagen, se puede ver claramente la consola central del sinfín, que ha trabajado en todos los cultivos durante las pruebas. En la imagen se puede ver el 3D VarioFlex 1070 AIR i (Komarno, Eslovaquia, 2017).
Hemos realizado pruebas de impacto en chasis híbridos y se aprobó que en caso que el cabezal golpee el obstáculo los que está dañado es la garganta de la cosechadora y tampoco el cabezal.
El módulo FLEX testado en 2017 en soja con dedos dobles y cuchillas BISO, incluido la trasmisión BISO.
Nuevas soluciones de diseño con los modelos ULTRALIGHT 800
A veces, la designación del modelo ULTRALIGHT 800 es un poco confusa, porque el número 800 no significa el ancho del corte, sino la extensión de la mesa vario en 80 cm. No solo se introdujo aluminio con esta línea de modelos, más precisamente aleación de aluminio. Con esta línea surgieron otras características constructivas que tuvieron éxito en la cosecha. Encolado de juntas, montaje central del sinfín continuo, accionamiento del sinfín desde ambos lados, molinete dividido y extensión extrema de los sistemas vario no solo hacia adelante, sino también hacia atrás hacia el sinfín. El nuevo cabezal fue presentato junto con el nuovo carro ProfiSteer con eje trasero orientable (dirección en las 4 ruedas).
El chasis rígido es esencial para un ajuste fácil y preciso del sinfín y para lograr un flujo suave del producto cosechado en la cosechadora. Las cosechadoras de rotor de alto rendimiento son particularmente sensibles a una alimentación suave.
3D VarioFlex: chasis híbrido con paralelogramo y módulo FLEX
El módulo FLEX se baja completamente a su posición más baja en la imagen.
Algunos cultivos de soja pueden ser un producto difícil a cosechar por el cabezal y por el maquilero.
La cosechadora con orugas está haciendo un trabajo perfecto. En la imagen se ve claramente el sistema VARIO ubicado debajo del chasis. Esta es una característica típica y una de las patentes clave de BISO utilizadas desde 2001.
Los nuevos cabezales 3D VARIOFLEX AIR i utilizan los chasis híbridos de los cortes Ultralight de tercera generación. Pero el departamento de investigación y desarrollo siguen desarrollando nuevas soluciones por lo tanto esto nuevo chasis está equipado hoy con el sistema FLEX a paralelogramos. El mercado también ha cambiado un poco durante este tiempo. Hoy, el ancho de corte de 10,7 metros se está convirtiendo en un estándar, mientras que las máquinas grandes buscan cabezales de corte de 12 metros.
Folleto en Español: http://navigator.biso.eu/en/en-biso/harvesting-technics/biso-3d-varioflex-air-i/
Durante la cosecha, decimos que la cosechadora funciona aproximadamente 22 días. Esto desarrolla una gran presión sobre los maquileros y los agricultores. Con un cabezal profesional, nuestros clientes pueden lograr una producción diaria de más de 100ha con cosechadoras como la New Holland CR9090SL SmartTrax. Para un cliente tan profesional, un chasis híbrido es un requisito fundamental para una larga vida útil de todos los componentes del corte.
Otros artículos interesantes:
BISO - SOJAFLEX
|
||
![]() |
BISO 3D VARIOFLEX•AIR•I Una cosecha eficiente y relajada comienza con un cabezal premium. Premium incluie modelos que pueden cosechar no solo cereales, colza o soja, sino también trigo |
|
![]() |
BISO 3D - COLZA, SOYA, CEREALES |